Why Do Back-Up Rings Fail in High-Pressure Applications? (A 2025 Guide)
July 18th , 2025
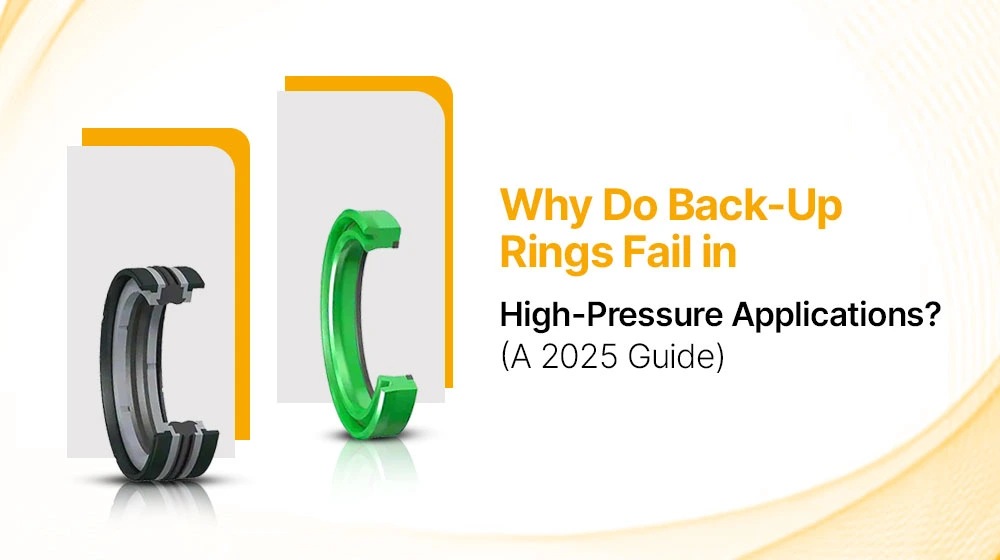
You’ve followed the right advice. The Back-up rings are in place. So why are the same failures coming back?
You’ve seen it before:
A machine is down again. Same unit, same leak, same seal. Your team replaced the O-rings just weeks ago, maybe even added a backup ring for extra support.
And yet, here you are. Another callout. Another delay. Another seal that didn’t last.
The issue often isn’t the part at all. It’s what’s happening around it – especially in high-pressure applications where groove dimensions and load shifts can quietly impact performance.
Here’s why failures keep happening even when you’ve done everything right, and what you can do to finally stop them for good.
Seal Failures Despite Back-Up Rings? Start with the Groove Design
A lot of the equipment in plants today was built years ago. The grooves in the cylinders or valve housings were made for just a seal, not a seal and a backup ring.
So, when a ring is added without changing the groove size, everything gets tight. Too tight.
What happens then?
- The seal gets compressed more than it should
- The back-up ring doesn't sit or work properly
- There’s no room for movement when pressure rises or temperatures shift
- That’s when things start to wear out quickly, even if both the seal and the ring are new.
If seals are wearing out too soon, check the groove. In many hydraulic sealing systems , incorrect groove dimensions are a leading cause of backup ring misalignment and eventual seal failure . A 10-minute measurement can explain what hours of troubleshooting don’t.
The seal and the back-up ring aren’t working as a pair
Just because the seal and the ring work, doesn’t mean they’ll work well together in your system.
We’ve seen this a lot:
- The ring is made from a rigid PTFE
- The seal is a soft elastomer
- The system runs hot, fast, and non-stop.
That rigid ring ends up pressing into the seal. The seal wears unevenly. Then it leaks. Then it fails. You know the cycle.
Watch how the materials behave in actual operating conditions and not just on paper. How they hold up under heat, repeated cycles, or long idle periods.
Sealing isn’t about ticking off technical specs; it’s about how well the parts move and perform together inside your system. Poor seal compatibility or mismatched materials in dynamic sealing conditions can quickly lead to O-ring extrusion and early failure.
System Upgrades Without Sealing Adjustments? That’s a Hidden Failure Loop
Let’s say the machine was reworked. A new pump was installed. Pressure was increased. Or the fluid was swapped for something more efficient. But no one reviewed the seal setup.
The system changed, but the sealing setup didn’t. And in high-pressure systems, that’s often where back-up rings quietly become ineffective, even if they were properly selected before.
Any time something changes, like fluid, pressure, load, or speed, revisit the sealing setup. It doesn’t take long. And it prevents weeks of repeated issues.
The Seal is New, But the Back-Up Ring Isn’t
This is a tough one because it’s usually done with good intentions. The seal fails. Maintenance replaces it. The backup ring looks okay, so it’s reused.
But over time, back-up rings lose their shape. They develop small cracks, lose flexibility, or can’t hold a shape after being compressed for too long. They may not look bad, but they’re no longer doing their job properly, a detail often overlooked in reliability engineering when focusing on reactive fixes.
The new seal sits next to a tired ring. It starts failing earlier than it should.
If the seal failed, then treat the backup ring as failed and compromised too, especially in high- pressure or high-duty systems. It’s not waste but prevention.
Standardising Rings Doesn’t Fit the Job
Having one backup ring spec across the plant simplifies things. They are easier to source, stock, and train around. And they also cost less than customising it. But not all systems are built the same.
For example:
- A slow-moving hydraulic press and a fast-cycling pneumatic actuator put different stresses on the seal.
- Some systems need split rings; others require solid rings to hold steady under pressure, especially when sealing under dynamic conditions found in many high-pressure applications.
When the same ring is used everywhere, it only truly fits some of the applications, and that’s where inconsistency and failure start showing up.
But you can still standardise it. Just make sure they are grouped better. Categorise the systems into different sets like dynamic, static, high-temp, etc., and get the rings accordingly.
You’ll still get the same sourcing and stocking efficiency, just without the unexpected failures.
Final Thoughts
You’ve already made back-up rings part of your sealing systems. That’s the right move.
But if your seals are still failing, this isn’t about changing parts again. It’s about checking if the system around those parts is helping or hurting them.
Sealing doesn’t work in isolation. The groove, the load, the fluid, the material, and the maintenance all play a role.
Once they’re in sync, failure stops being a routine event and becomes a rare one.
Need a fresh set of eyes on your sealing system?
We work with engineers and maintenance teams every day to review groove designs, material fit, and real-world performance and not just the catalogue specs.
If the failures haven’t stopped, there’s probably something simple being overlooked. Let’s fix it together.
Not sure if your back-up rings are right for your equipment or pressure conditions? Reach out to Arvi Hitech today and let our team help you review what fits and what could be costing you uptime.