Why Your Pneumatic System Keeps Leaking and How to Design It Leak-Free
July 17th , 2025
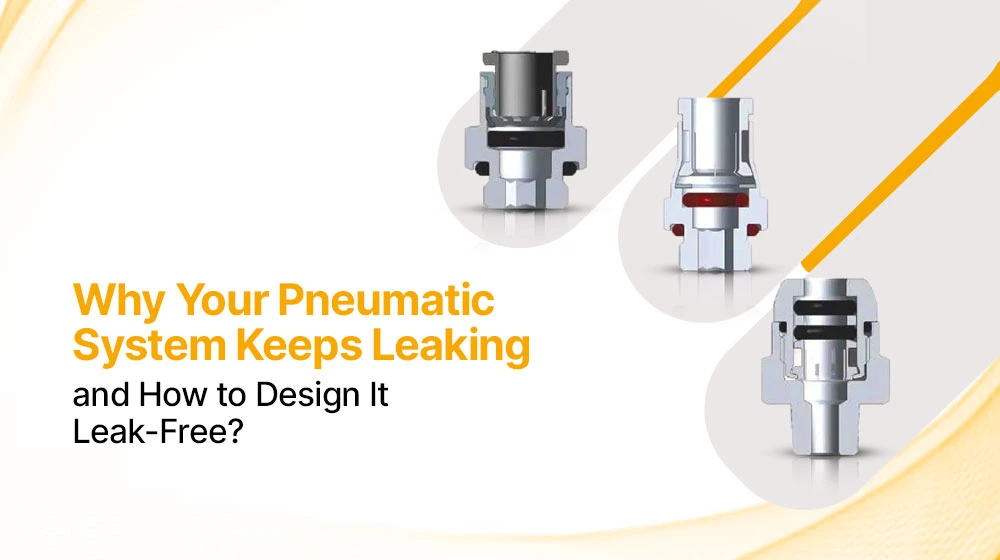
If you’re always chasing leaks, stop blaming the leak. Start blaming the design.
Leaks happen. Especially in pneumatics. Especially in places with heat, vibration, or improper installation. But when they keep coming back, that’s not just wear and tear anymore. That’s a bigger issue. Be it a pneumatic actuator, valve, fitting, or seal, leaks show up, get patched, and then come back. The cycle continues.
You might think that it’s okay and just neglect it. And that’s where things start going wrong. If leaks keep returning, they’re not a maintenance issue anymore but a design issue.
You can keep replacing parts. You can keep tightening fittings. But if the system wasn’t designed and built with your process in mind, with the right materials, right tolerances, and right conditions, those leaks won’t stop. They’ll just move.
You don’t get leaks because someone overtightened a fitting. You get leaks because someone fitted the wrong specification a few months ago. They start way before installation, at the sourcing and system design stage.
In this guide, we’ll explore what causes the leaks and how to design a leak-free pneumatic system that holds up under real-world operating conditions.
What’s Causing The Leaks in Your Pneumatic System
In pneumatic systems, leaks don’t just happen because of bad luck or wear and tear. They happen because something in the system doesn’t belong or doesn’t work the way it should under real-world conditions.
Most of the time, it comes down to one thing – poor compatibility between parts.
Here’s what usually goes wrong:
- Mismatched materials Just because a seal looks good on paper doesn’t mean it survives chemical exposure, thermal cycling, and 14-hour shifts. That causes the system to break down sooner than you think. And once it does, the leak follows.
- Thread or tolerance issues One fitting is off by half a thread. One port isn’t cut clean. And that’s it - pressure loss. And you won't find it with the naked eye. This is what happens when you source your parts from various vendors.
- Surface finish problems Even if the part is dimensionally correct, the surface finish might not be right. A seal can’t seat properly if the cavity it sits in isn’t smooth or machined to the required specifications. That’s another weak point, waiting for the leak to happen.
- Assembling mistakes Over-tightening. Under-tightening. Skipping lubrication. Ignoring torque specs. These might seem like small errors, but they’re not. Even one misstep during the assembly can turn into a recurring maintenance headache.
And the tricky part?
These issues don’t show up right away. Everything seems fine at first. The system runs. Then weeks or months later, the leaks start.
And by then, you’re no longer fixing a part; you’re chasing a flaw that was built into the system from the start.
How to Design a Leak-Free Pneumatic System
You can’t test quality into a system. It has to be designed-in from the start. If your setup is leaking, it’s not bad luck—it’s telling you something was missed or compromised in the design stage.
Here’s how to get it right the first time.
1. Start with Specification, Not Assumptions : Most leaks aren’t random. They’re in there early, but only show up when real conditions get overlooked. Design for what your system actually sees – pressure swings, heat, chemicals, and cycle load. Don’t go by the catalogue specifications; instead, choose what actually fits your system.
2. Use Components That Were Meant to Work Together : It’s easy to assemble a system from multiple vendors. But mismatched threads, seals, or finishes guarantee the failure. If the components don’t share the same tolerances, material standards, or sealing approach, leaks become inevitable. Choose a unified platform, thread type, sealing method, and proven combination for a leak-free system.
3. Assembly Isn’t Just a Step. It’s a Risk Factor : You can make every part perfectly and still end up with leaks, because of how it’s assembled. When the assembly goes wrong, the pressure tolerance weakens, which leads to downtime. When assembly’s done right, your system can run smoothly for years, with minimal maintenance. Following best practices in pneumatic system design helps ensure consistent sealing and long-term performance.
4. Design for the People Who’ll Service It : Leaks often show up after the first repair, not the first build. And when maintenance is hard, you take shortcuts. If you have to disassemble half the system to change a gasket, the odds of reassembly mistakes go way up. And the leak you thought you fixed just moved.
5. Test Like It’s Going Into Production : Just because a system holds pressure on day one doesn’t mean it’s ready for the real world. If it’s going to go through vibration, heat, cycling, or aggressive media, it needs to be tested in those conditions. Otherwise, you’re not validating anything. Catch the failures before your process does.
Critical Questions Every Facility Manager Should Be Asking
Leaks aren’t always about the part that failed; they’re often about the questions no one asked before installation.
Ask these questions before getting the parts and seal for your system –
- Does this part match our actual process conditions?
That means pressure, temperature, and media, not just what's in stock or “close enough.” - Is this part rated well above our normal operating range?
Running close to the limit isn’t efficient. It’s risky. - Is the material compatible with our gas, lubricant, or cleaning chemicals?
Some seals break down slowly. Others fail suddenly. Either way, leaks follow. - Are the threads and tolerances consistent with the rest of the system?
Even tiny mismatches, the ones you’d never notice by eye, can become leak points once the system’s under pressure.
Conclusion
If your system keeps leaking, stop fixing fittings. Start fixing the decisions that put them there
Replacing a fitting might stop the leak for now, but it’s not fixing the reason it happened in the first place. The real fix starts earlier—with better choices, tighter specs, and parts that actually belong together.
If you’re constantly chasing leaks, it’s time to step back and ask why they keep happening. Because a system that’s designed right doesn’t need constant fixing.
At Arvi Hitech , we source genuine Parker components, selected to fit your system the way they should.
If you’re tired of fixing the same leak twice, we’ll help you build it right the first time. Let’s talk.